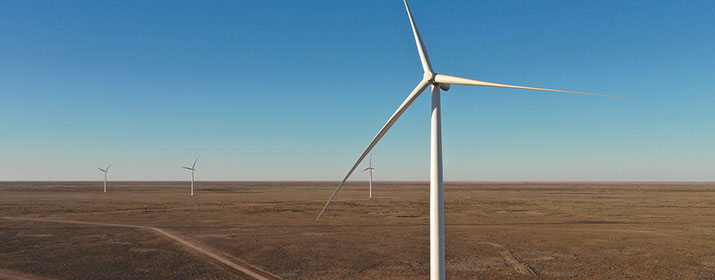
Serving local customers with wind power from New Mexico requires both advanced technology and old-fashioned hard work.
TEP’s highly trained technicians are using new acoustic sensors and drones to monitor operations and speed up repairs at our Oso Grande Wind farm in southeast New Mexico.
The site, which started producing clean energy for us in 2021, includes 62 turbines located on 24,000 acres of barren, wind-swept desert. The 250-megawatt (MW) system is our largest renewable resource, designed to generate enough power each year to serve the annual electric needs of nearly 100,000 homes.
The site was chosen for its strong wind, particularly during the morning, evening and overnight when solar arrays produce little or no power. Winds regularly reach speeds of 15-30 mph. Some wind turbines at the site are nearly 600 feet tall from base to blade tip.
Although its location offers strong wind resources, Oso Grande is also subject to powerful thunderstorms and lightning strikes that can damage units.
“We’re watching our systems all the time to make sure each unit is running as smoothly as possible,” said TEP’s Michael Bryan, Asset Manager for Oso Grande. “And if we detect a problem, we’ll respond as quickly as possible to minimize damage and to get each unit up and running again.”
To improve blade monitoring, audio sensors are affixed to each wind turbine. The sensors record and analyze the sound of each unit’s operation to monitor for acoustic anomalies that indicate blade damage.
The sensors also detect electromagnetic fields generated by lightning strikes. If a lightning strike occurs, the time and location are provided to TEP within 30 minutes of the event.
The data allows TEP to dispatch resources efficiently. This helps us make repairs more quickly, particularly since our turbines are installed across an area as large as 20,000 football fields, or the size of Florida’s Walt Disney World Resort. Bryan said the monitors were critical last year after a powerful thunderstorm blew through the area.
“The acoustic sensors indicated there was a problem with one of the turbines, so we paused its operations and performed a repair. We placed the tower back into operation, but sensors suggested there was also damage to one of the unit’s blades,” Bryan said. “Each blade is hundreds of feet long and stands hundreds of feet in the air, so we used a drone to take a closer look.”
The unit was taken out of service after technicians found a crack in one of the blades. Bryan said around-the-clock monitoring and the audio sensors help technicians focus their efforts more effectively so that each unit can operate smoothly and produce as much power as possible.
In addition to the acoustic sensors, weather instrumentation at the very top of each turbine monitors wind speed and direction. The data is used to automatically adjust the direction of each turbine, which generate power at speeds beginning around 5 mph and up to about 55 mph.
As wind speeds increase, turbine system controls can make automatic adjustments to regulate power output while reducing strain on the turbine. If the winds become too powerful, the pitch of each blade will adjust automatically to reduce wind load. In strong sustained winds, turbines can even cease operations to prevent damage.
At any given time, one or two units at Oso Grande will be out of service for preventive and routine maintenance or to repair other damage.